Metal Casting Quality Standards
The most important aspect in guaranteeing the reliability of a precision investment cast component is a casting quality verification process that is both meticulous and detail oriented. When rigorous and comprehensive metal casting inspection methods are combined with increased metal casting quality standards, part production quality and performance is enhanced. At Aero Metals, we employ world class methods in the inspection of casting to create high performance parts and components.
Metal Casting Inspection Methods
At Aero Metals, we provide the following metal casting quality inspection methods to ensure every part and component we manufacture meets our high level of expectation and our customers receive the finest cast parts and components in the industry.
1. Visual Inspections
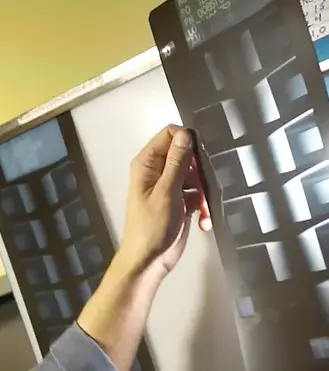
Our casting quality control experts utilize visual techniques to ensure parts are properly filled with metal (no cracking, tearing, holes or voids, non-fill, etc.). They also meticulously inspect each part, making sure there are no distortions or bends before moving forward in the casting quality process. During the final phase of inspection, parts are inspected and compared to the casting quality control plan and written process instructions. Lastly, the casting quality results are documented and stored for future use by production department staff and process engineers.
2. Mechanical Properties Inspections
To confirm the properties of the metal cast part are correct, mechanical testing is performed to approve the metal of the casting. The testing confirms the properties comply per the specified mechanical requirements. The following mechanical properties testing methods are performed to confirm proper casting quality.
- Hardness testing - A non-destructive procedure that demonstrates the alloy’s machinability and wear resistance.
- Tensile testing - A destructive casting quality test that provides ultimate tensile strength, yield strength, elongation and reduction of the material test specimen.
- Load testing - This test is performed on the entire casting lot to evaluate its casting quality, and to verify that the cast part can carry (deflect) the required or specified structural load when applied. Pressure-containing parts can be hydraulically tested to a proof load or destruction maximum limit.
3. Dimensional Inspections
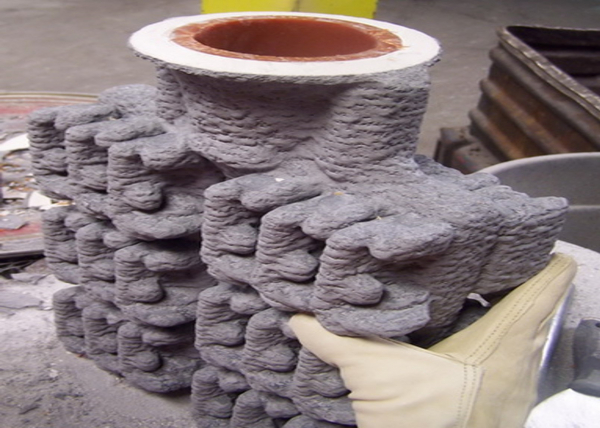
Our experts utilize Investment Cast Industry Standards as a guide by setting a range of values the casting dimensions can fall within. We also take into consideration critical part dimensions, given to us by the customer, during the planning and inspection phases. We then verify the dimensions of the parts by using micrometers, thread and plug gauges, CMM machine, and other approved functional gauges. The accuracy of these measuring tools adds to the dimensional consistency and casting quality of the manufactured parts.
4. Chemical Inspections
Aero Metals currently uses x-ray fluorescence (XRF) analysis machine [spectrometer] in its metallurgy lab. Before the metal is poured from the melting pot, a sample of molten metal is poured in to a small “coupon” mold and the casting quality is evaluated in the spectrometer. If needed, minor alloying elements are added to the material to bring the alloy melt into required specification. Then another coupon is tested and certified to ensure proper chemical composition.
The chemical composition of every alloy melt is tested and recorded in our database. We then electronically store the records for an indefinite period. This test is performed to ensure the alloy performance properties are to the specification(s) of the customer. Casting alloys are typically specified per ASTM, AMS and SAE alloy specifications.
NDT & Other On-Site Metal Casting Inspection Methods
American Metal Testing is our sister company, where we conduct Non-Destructive Metal Testing (NDT) in-house. The NDT process helps to ensure a casting’s quality without destroying it. AMT offers additional services to Aero Metal’s investment casting on-site, such as testing, inspection, and quality assurance.
American Metal Testing is NADCAP Certified in the following processes:
Non-destructive testing helps to ensure product quality and can be required in some leading industries, including military & defense, automotive, and aerospace. If you are considering quality testing and other add-on services, visit AMT’s website for more information on non-destructive metal testing options for your application.
Quality Metal Castings by Aero Metals
Aero Metals offers a wide variety of in-house casting quality control, verification and product testing services (such as NDT) designed to provide our customers with the highest quality cast product. No matter what the intended application, every precision investment cast component is examined, inspected, and approved before leaving our building.
Contact us for more information regarding our metal casting inspection methods, or call us at 219-326-1976 and we will gladly answer any questions that you may have. Aero Metals is your trusted resource for proven metal casting quality for high performance metal parts.