Investment Casting
At Aero Metals, we specialize in delivering high-quality, near-net-shape castings that meet the most demanding industry standards. Whether you need complex geometries, tight tolerances, or a smooth surface finish, our investment casting services provide unmatched accuracy and cost efficiency.
Aero Metals works with you to produce high-quality investment castings to your project specifications. Check out our featured cast parts gallery for examples of our precision casting capabilities, or request a quote today.
Premium Investment Casting Material Options
With more than 220 different ferrous and non-ferrous casting alloys available, Aero Metals can produce metal castings using its extensive range of metal alloys for unlimited metal investment casting applications. The metal investment casting process is very versatile and produces a broad spectrum of metal cast assemblies for a wide variety of industries. Investment cast metal parts provide the maximum design flexibility for manufacturing complex, one-part components.
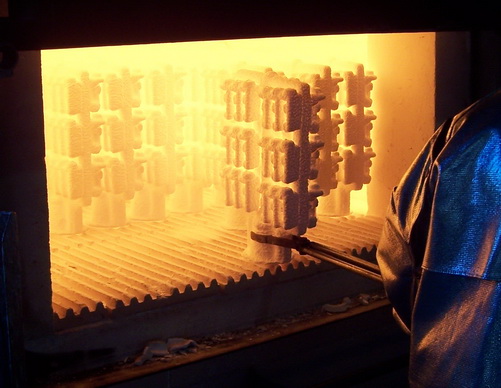
At Aero Metals, we produce complex parts from a wide range of investment casting alloys. Our team is committed to quality precision investment casting, and we work with a variety of metals to produce components to your exact specifications. Available precision casting alloys include:
- Stainless Steel
- Steel
- Ductile Iron
- Beryllium Cooper
- Nickel-Based Alloys
- Aluminum
- Cobalt-Based Alloys
- Copper-Based Alloys
In-House Wax Injection Molding and Additional Capabilities
Aero Metals produces its wax injection molds in-house and maintains them free of charge for the life of the program. We utilize the latest solidification software technology and innovative practices to ensure consistent and precise wax patterns when manufacturing your cast metal parts. Additional investment casting capabilities include:
Investment Casting ERP Tracking System
The metal investment cast process at Aero Metals is tracked through a state-of-the-art ERP system, monitoring our production to ensure quality and reliable metal casting throughput and process controls. We also adhere to our certified ISO quality procedures to deliver repeatability from lot to lot.
Metal Precision Casting Industries Served
Aero Metals has been serving customers across numerous industries for over 60 years. Our commitment to quality meets and exceeds any industry standards. From firearm parts to pump and valve castings, we help solve your cost-performance challenges and work with you to develop a trusted design that meets your requirements. Some of the industries Aero Metals serves include:
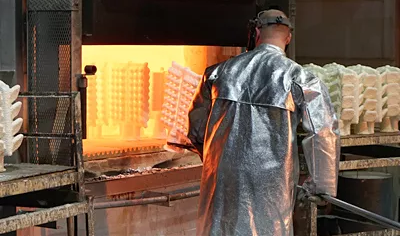
- Aerospace
- Military & Defense Casting Parts
- Door & Lock Security Hardware
- Agricultural, Industrial & other Heavy Equipment
- Medical Devices & Equipment
- Hand Tools & Power Equipment
- Automotive/Truck Parts
- Marine
- And many more!
Why Choose Investment Casting Over Other Methods?
You may be wondering why you should choose precision investment casting over other metal fabrication methods. We’ve developed some helpful charts to compare metal casting methods. These resources demonstrate why investment casting may be a better choice, preventing excessive tooling and saving you time and money.
There are many benefits to the investment casting process, including:
- Lower tooling costs
- Tight tolerance control
- Waste reduction
- Reliability
- Value-added design
Why Choose Aero Metals as Your Investment Casting Foundry
Whether it's a high-volume run or a recurring order to help maintain your inventory, Aero Metals has the equipment, the experts, and the experience to help you succeed. We have been casting metal parts through the investment casting process for over 60 years.
Our world-class 175,000-square-foot facility features the industry’s most technologically advanced equipment. We would be happy to consult with you and provide direct design assistance for your next metal investment casting project. Our results-driven expert team offers the following approach to your investment casting needs.
- Engineering centric with a metal casting focus
- Custom-designed tools built in-house
- Extensive experience with complex geometries and hard-to-manufacture parts
- Capable of handling high-volume investment casting production runs
- Numerous material options, including ferrous and non-ferrous alloys
- In-house CNC machining capabilities
- One-stop shop for investment castings and casting-based assemblies
- Guaranteed consistent quality
Contact Us to Learn More About Precision Investment Casting Today
Contact us for more information regarding our metal investment casting options, or call us at 219-326-1976. Our experienced team will gladly answer any questions you have. Aero Metals is your trusted resource for high-quality and high-volume investment casting metal parts.